General Information
General features
- Plastherm PPRC pipes and fittings are produced from Polypropylene Random Copolymer raw material, produced for hot and cold water installation applications.
- Thanks to the durability of PPRC pipes and their high performance in compressed air tests, they can be used safely for industrial applications.
- Produced in accordance with ISO 15874, DIN 8077, DVGW standards, Plastherm PPRC pipes and fittings are suitable for hot and cold water installations and industrial use.
- The service life of Plastherm PPRC pipes and fittings is more than 50 years under recommended conditions of use.
- PPRC pipes are useful in indoor hot and cold water installations due to their hygienic, easy installation and application and low cost. Aluminum foiled pipes and glass fiber reinforced pipes especially produced for combi boilers and heating installations provides energy efficiency. Due to the low thermal expansion of foiled and glass fiber reinforced pipes, there is no physical change in the pipes during use.
- Our products are resistant to all kinds of external factors, since they are produced from Polypropylene Homopolymer and Polypropylene Random Copolymer raw materials of world-class raw material producers.
- PPRC PIPES
- ALUMINUM FOILED PIPES
- GLASS FIBER REINFORCED PIPES
PPRC Pipe Advantages
- PPRC pipes do not change the taste, odor and color of the water.
- It does not leak or leak because it is assembled by adhesion method.
- Due to the characteristics of the raw material, a situation such as rotting or rust never occurs.
- Thanks to its smooth surface, it does not deposit or deposit, thus preventing the formation of currents and bacteria.
- Diameter and wall thickness wear is not possible, it prevents lime formation.
- Their lifetime is more than 50+ years under recommended usage and assembly conditions.
- It is resistant to high temperatures and does not lose its function.
- Among the accepted values, it is resistant to all kinds of acidic or basic chemicals.
Technical Specifications of PPRC Hammaddes
- It is manufactured using polypropylene raw material and aluminum foil coating. The heat transfer is controlled by covering the middle layer of thin aluminum foil.
- Provides heat and energy efficiency in heating and hot water installations.
- When it encounters hot water, it does not physically change the pipe length and it does not elongate and sag in the pipe length.
- With the special pipe stripping apparatus used, the area to be welded can be peeled off and easily welded to additional parts in a short time.
- The elongation coefficient is 0.030mm / mK.
- Its thermal conductivity is 0.24 W / mK.
PPR Glass Fiber Reinforced Composite Pipes
- Produced in 3 layers, these pipes consist of polypropylene raw material inside and outside and glass fiber polypropylene in the middle part. Production is made in PN20 and PN25 wall thicknesses according to customer preference.
- Plastherm glass fiber reinforced PP-R pipes can be easily used in the areas where foiled pipes are used, as they have a heat expansion coefficient close to the performance of foiled pipes.
- Expansion and sagging are at minimum level.
- It does not require trimming like foiled pipes during assembly of glass fiber reinforced pipes. It can be welded like normal PPR-C pipes.
- Ideal for all central heating and hot water installations.
- The elongation coefficient is 0.035 mm / mK.
- Its thermal conductivity is 0.24 W / mK.
Expansion Calculation in Pipes
Matters to be Considered in the Installation of PPR Pipes and Fittings
- The installation should be properly tested with 1.5 times the system pressure (20 bar).
- For bends over 30°, a 45° bend should be used.
- Pipes should not be cut with any tools other than pipe scissors.
- After the installation is installed, UV rays coming on the installation should be isolated.
- Avoid pipes and fittings from direct sunlight. Keep the materials indoors.
- Hard impacts can cause invisible capillary cracks in PPR pipes and fittings.
- Therefore, it is necessary to be careful during assembly and transportation.
- Do not use products whose outer surface is deformed for some reason.
- Use after cleaning the products that are dirty during installation or have gotten dirt inside the pipe.
- During the assembly of fittings, tighten metal products when dark:
- Do not use fire to shape the pipes. Continue with the required additional parts.
- We recommend that you use Teflon during the assembly of additional parts.
- Welding should be done by taking precautions at temperatures below + 5C. In welding performed at low temperatures, the material hardens and its crystal structure deteriorates and a smooth welding will not occur.
- Sudden temperature changes may cause cracks in pipes and fittings. • Since polypropylene materials are flammable, keep them away from fire.
- If mounting with clamps, expansion and directional changes should be calculated.
- If the pipe length to be applied is long, bending and bending calculations should be made.
- Pipe clamps should be mounted in a way that does not prevent expansion.
- The water in the system must be drained in freezing temperatures. Otherwise, there may be cracks and explosions in the pipes. After the installation is completed, a test must be done before starting the system.
- Plastherm pipes should only be assembled with Plastherm fittings. Products of different brands should not be used.
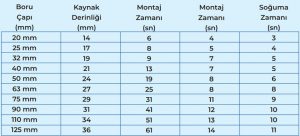
Important Technical Issues in PPR Pipes and Fittings
- Flexing Pipe and Its Calculation
- Fixed Support and Calculation Clamp Distances
- Pipe Bend Diameter insulation
- Pressure Test
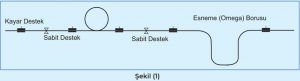
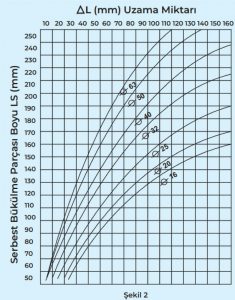
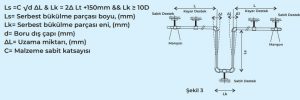
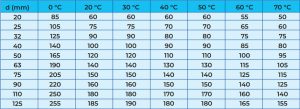
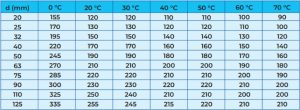

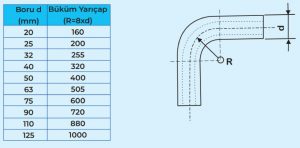
Considerations About Insulation in PPR Pipes
Metal or galvanized installations require more filling material and insulation than polypropylene installations. Polypropylene materials seem to be self-insulated because of their low thermal conductivity. There is no need for isolation under normal conditions in PPR installations made inside the building. This self-isolating condition is the biggest factor in minimizing the wall thickness of the pipe and the reinforcement materials used, glass fiber and aluminum foil, to the heat conductivity. However, the place where the system is laid and the size of the system are also very important.
Insulation is required to prevent frost and heat loss in hot water pipes. If the installation is made in the external environment or if a part of the system passes through the external environment, that part must be isolated and protected against frost in the winter months. Likewise, if the hot water installation is to be applied longer than the calculated one, the places where the hot water installation passes should be isolated with filling or insulation materials in order to prevent heat loss.
It is necessary to take measures against weather conditions in the pipes laid outdoors. Insulation materials will also protect the pipes from external factors. Approximate calculations of the insulation to be made in PPR, foiled and glass fiber reinforced pipes are given in the tables below.
Insulation thickness for Plastherm PN 20 pipe
Insulation Thickness for Plastherm Foiled PN 20 Pipe
Plastherm Glass Fiber PN 20 Insulation Thickness For Pipe
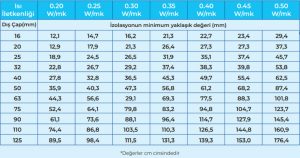
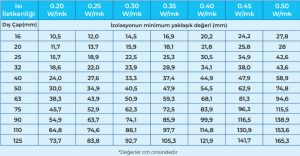
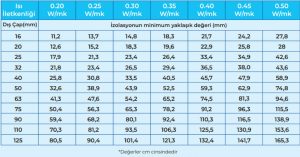
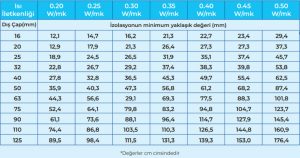
Final Stage Pressure Test
- After the hot or cold water installation application is completed, it must be subjected to a pressure test. This test should be 1.5 times the pressure to be used. It should not be forgotten that the factor affecting the pressure due to the expansion in the pipe as a result of the temperature change in the environment. A temperature change of 10 ° C creates a pressure difference of 0.5 to 1 Bar in the system.
- After the installation is completed, the system is filled with water and pressure and leakage tests are performed. The air of the system is automatically taken with the intermediate element parts placed at the end or the top points of the system, or the system is pressure tested with the pump after the end points of the system are closed with a blind plug.
- Pressure test consists of 3 stages. In the first stage, 30 minutes to the system. It is tested with a pressure value of 1.5 times throughout. Meanwhile, every 10 minutes. The system pressure in it is reduced to its previous state and increased again to the value 1.5 times. Pressure drop up to 0.6 bar or it should not be ascending so that it is understood that there is no leakage or leakage in the system.
- In the second stage, the same process should be done for a longer time. It takes approximately 2 hours.
- In the last stage, the resistance and strength of the system are measured by applying the same test in a much more series between 1 and 10 bars. This is based on sudden changes and the pressure test of the system is positive if there are no leaks or leaks in the system.
- These tests should be done with a pressure measuring device with an accuracy of 0.1 bar.